Linfox Resources & Industrial – Injury Prevention Program
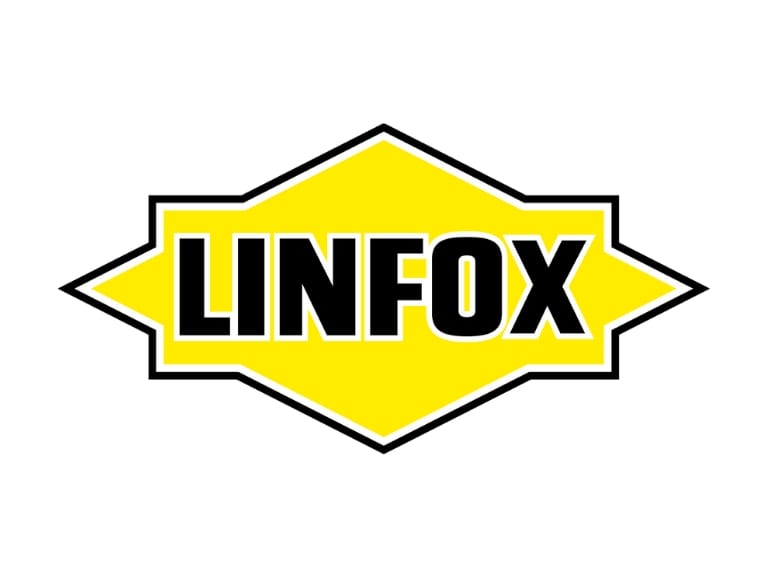
Linfox Resources and Industrial provides specialised logistics services to the resources, mining, oil and gas, industrial and infrastructure sectors. Their industry experts design bespoke, land-based logistics solutions including general freight, on-demand project services, 24/7 emergency breakdown logistics, and bulk commodity haulage for the mining, oil and gas, heavy OEM and industrial sectors. Their capabilities include bulk liquids, bulk haulage, dangerous goods, warehousing and distribution, industrial warehousing and transport, production support logistics, remote logistics.
The Challenge
In August 2023, Linfox approached KINNECT for an injury prevention program to reduce the high number of musculoskeletal injuries being sustained at their Dulux warehouse site in New South Wales.
They had tried three approaches in the past, none of which had delivered significant or sustained improvements to the rate of injury. Firstly, prior to COVID-19, Linfox provided an onsite physiotherapist. While this early intervention service was well-used by employees, it was targeted at relieving symptoms, rather than addressing the root cause of the problem – their manual handling technique.
Secondly, Linfox had engaged providers in the past to run manual handling training, however the programs weren’t tailored the specific tasks that workers performed on the job which made it difficult for the workers to apply the training. Off the shelf manual handling programs are most effective when people are lifting the same type of boxes in a consistent environment, however when there are variables in play in terms of environment, equipment and materials, more specific techniques are required.
Thirdly, Linfox had a pre-start warm up and stretching program, however workers weren’t getting the full benefit as they completed the exercises too quickly, and there weren’t sufficient dynamic activities to warm up their muscles. They also weren’t stretching during the day if they experienced stiffness or soreness.
Linfox needed a customised solution that could be directly applied to the workers roles, for example, lifting a paint tin, wrapping a pallet, lifting gates or pulling curtains on a truck. Furthermore, both the theoretical and practical content needed to reflect the specifics of their tasks.
Objectives
In the 2022-23 financial year, 26 out of Linfox R&I’s total 38 recordable injuries were sprains and strains. Eight of these recordable injuries were from the Linfox Dulux site, with seven out of eight recorded as slips, strains or sprains.
While no specific targets were set, Linfox had an overall goal to see the trend of musculoskeletal injuries go down as quickly as possible.
Solution
Kerry Chiu, KINNECT Lead Consultant and Accredited Exercise Physiologist met onsite with Linfox managers and team leaders to assess the different tasks being completed and the general working environment.
Then, working with the National Safety and Compliance Manager, a multi-part injury prevention program was devised. It included:
Part 1: Manual Handling Training
KINNECT created a customised version of our existing program that met their specific needs with a presentation featuring photographs of their own staff. The training session encompassed the KINNECT 4 rules for safe work:
- Work safe and healthy
- Own your health
- Risk responsibility
- Know your lifting techniques
Part 2: Warm Up & Stretching Programs
A series of job-specific warm up exercises and stretches were selected for completion during pre-start and also throughout the day, aimed at minimising their workforce’s potential risk of soft tissue injury. Workers were trained to perform these exercises and stretches properly, and the presentation slides featuring their own staff were printed and displayed throughout the site.
Part 3: Train the Trainer Sessions for Managers, Team Leaders and Champions
This training ensured that they were able to lead pre-start warm-ups themselves, educate their teams on manual handling principles and incorporate skills into the onboarding process to ensure the longevity of the program. The training sessions included:
- Manual handling principles
- Tissue fatigue
- Risk Identification
- Warm up Activities
- Benefits of warming up
- When and What to Stretch
- Warm Up Movements & Dynamic Stretch Program
- Static Stretch Program
- Practical Exercises
After the training, Kerry remained onsite for two weeks to provide workers with live feedback and coach them on manual handling techniques as they worked. He developed a great rapport with the staff as he attempted tasks himself and asked them to show him how to do them correctly.
Results & Benefits
This program was successful in reducing recordable work injuries from eight in FY23 (seven of which were related to sprains, trips, slips and falls during manual handling tasks) to two in FY24, both of which occurred prior to the implementation of KINNECT’s injury prevention program.’
Linfox were keen to maintain this progress and invited KINNECT to run a refresher in November 2024 for new and existing staff.
Not only were there less injuries, but the program itself received positive feedback from participants, including:
- We now do startups differently, and they are better
- Thought it would be more of the same, but I really enjoyed the training
- Showed me new techniques and how to look after myself.
- As someone with a back problem this was really informative. I correct my team if they are doing it wrong.
- I really like the overhead stretch and do it every 15 minutes or so.
One worker offered this unsolicited feedback:
“This really was the best course on this topic I’ve ever completed. I learned new techniques about resetting muscle fatigue.
The trainer Kerry was upbeat and likeable. The examples given were straightforward and easy to understand. Physically holding the [jelly] snake and marshmallow while seeing in detail on a screen what they represent was really eye opening.
I immediately put some of these suggestions to use while driving to Newcastle and absolutely noticed a difference.
All in all, I learned that small changes can have a huge impact on my body.” – Mike, Driver.
We also received this feedback from the Site Operations Manager:
“As someone who personally exercises in my spare time, I naively went in with the mentality everything in the training would be common knowledge and it was just another course that we have to sign off on. I am proud to admit that the training I experienced was excellent value and completely surprised me how much it was needed as throughout the training I looked to my peers and noticed how not so common the knowledge of correct form was even, amongst our leadership here on site. From what I experienced I strongly believe this was needed here and would certainly suggest something like this be rolled out across the network.
Sessions were very informative and gave everyone an explanation on the benefits of doing lifts a certain way.
The team took on the sessions very well. The sessions were something different to their normal everyday duties and a bit of a change from these duties kind of refreshed them.
The sessions got the team together. Most roles in the warehouse such a picking or replenishing are pretty individual roles so it was great that they could do an activity in a group. All in all, the team seemed very happy and engaged.”
Ready to partner with KINNECT?
Request a Service
Know what you need from us? Request a service from us right now.
Locate us
Have a need in a particular location? View our service capabilities throughout Australia.